Reactive hot melts – bonding in two stages
Reactive hot melts – bonding in two stages
Bonding with reactive hot-melt adhesives is not that complicated if you take into account the way the adhesives work.
The way these adhesives work is based on a clever combination of two main components. First, there is the thermoplastic base, which allows the adhesive to melt and turn into a liquid state when heated. With this component, you can achieve a rapid build-up of strength and rapid handling stability. This enables quick and easy application on the surfaces to be joined, which is particularly advantageous in automated processes.
The second component is made up of reactive groups that are responsible for curing or cross-linking the adhesive. This chemical reaction leads to a permanent connection and, depending on the type of reactive groups (isocyanates / silanes), the chemical reaction can vary.
Process of chemical cross-linking
The chemical cross-linking takes place in two stages. First, the adhesive is applied in a liquid state to the surfaces to be joined. While the adhesive is still liquid, the substrates to be bonded are joined together. In the first stage a physical setting mechanism occurs that provides sufficient strength for further processing or transportation. This is known as handling stability.
In the second stage, which can last from hours to several days depending on the reactive group, chemical cross-linking takes place. This chemical reaction depends on the moisture supply and accessibility of the adhesive joint to atmospheric moisture.After the hot-melt adhesive has fully reacted, it loses its thermoplastic properties, i.e. it will not become soft again, even if the glued object heats up.
The advantages of reactive hot-melt adhesives are impressive. They offer extremely good adhesion values on a wide range of materials, including metals, plastics and other substrates. Their high strength makes them ideal for applications where strong and durable bonds are required. In addition, they are temperature-resistant and offer good solvent resistance, as well as high aging resistance.
Airtight packaging
From cartridges to drums, we offer a variety of packaging options that can be processed using our purpose-built melt tank equipment, such as bag melters or drum melters.
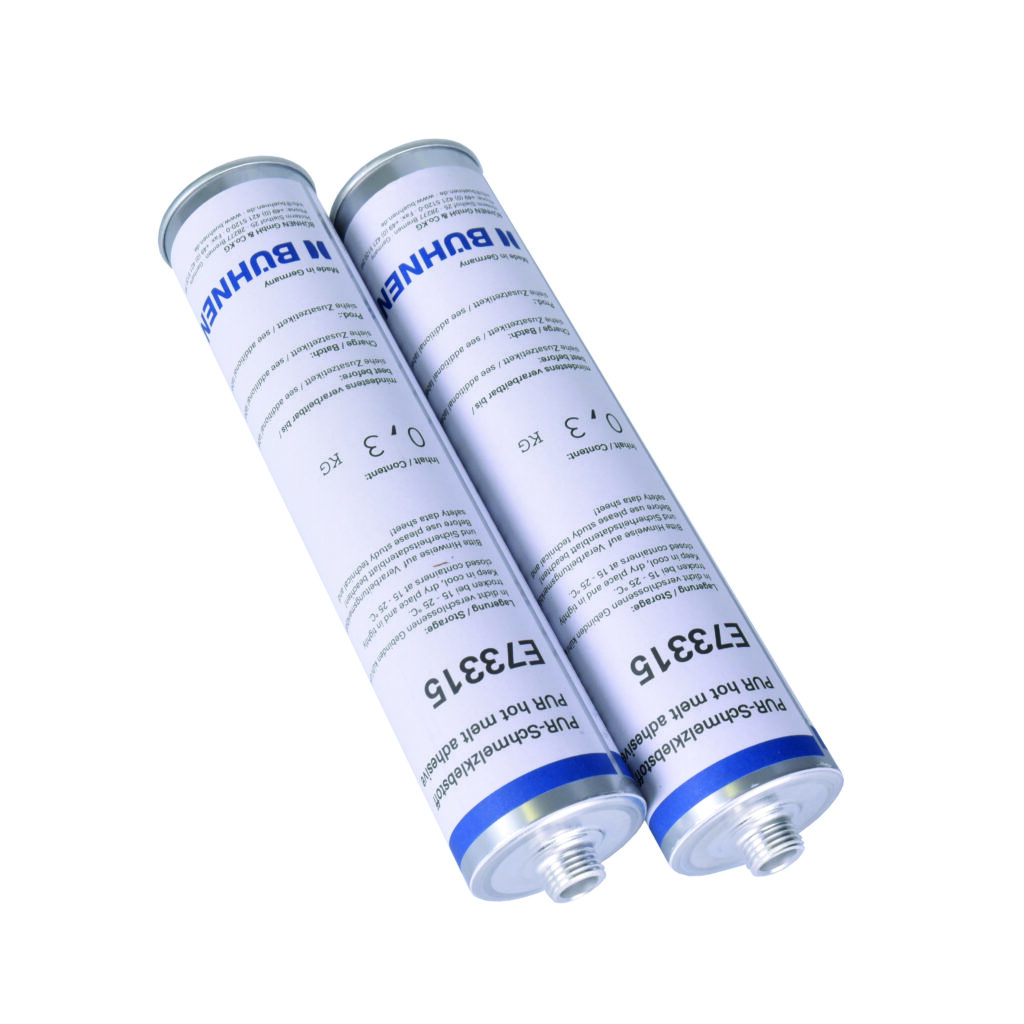
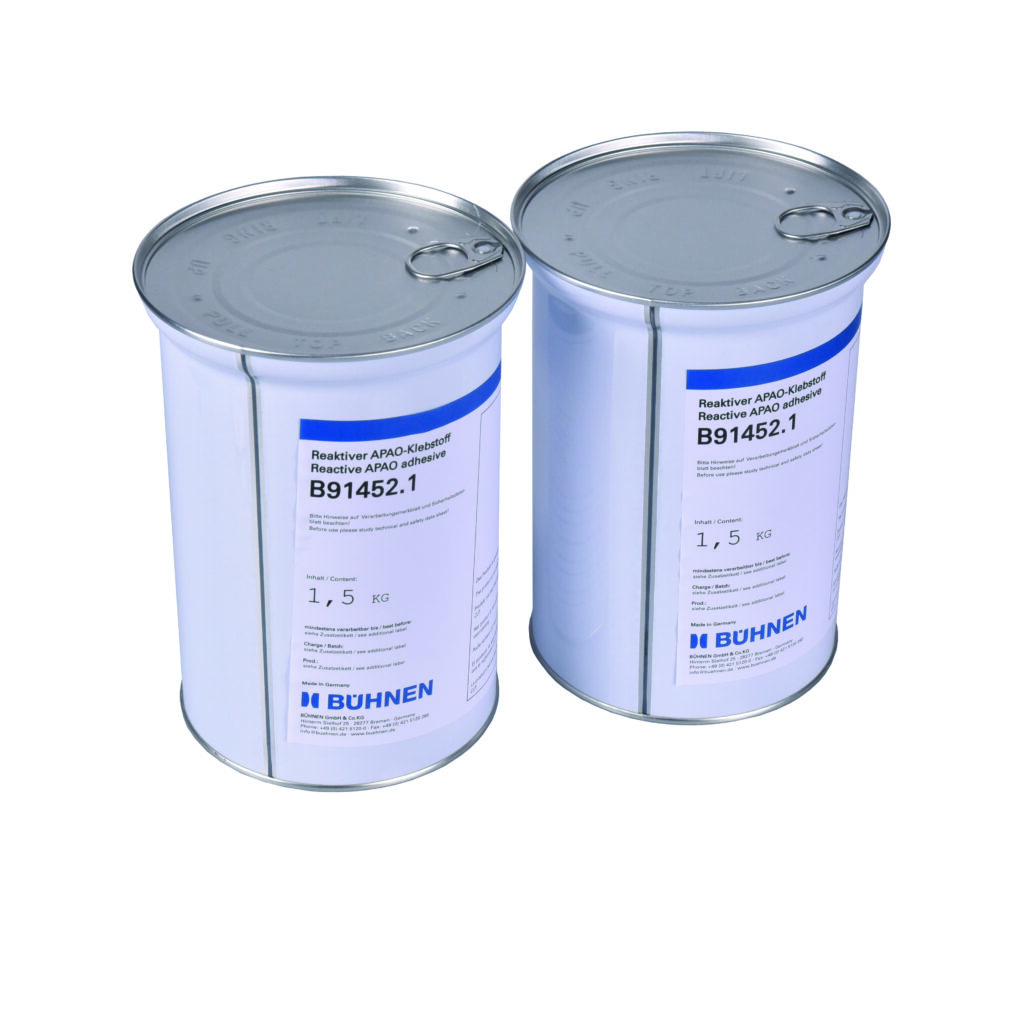
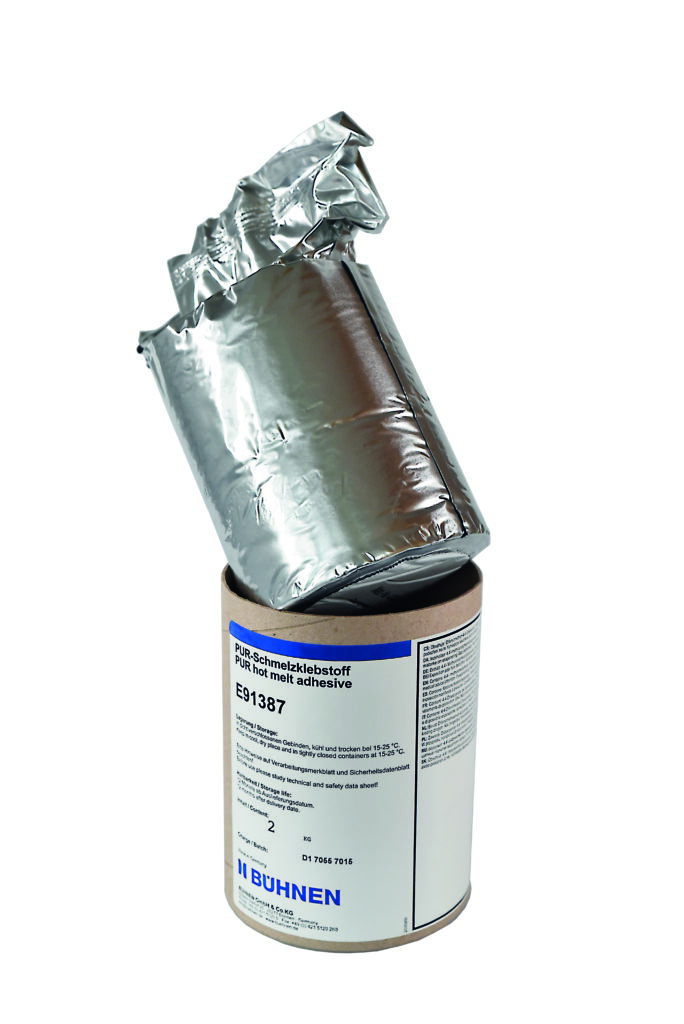
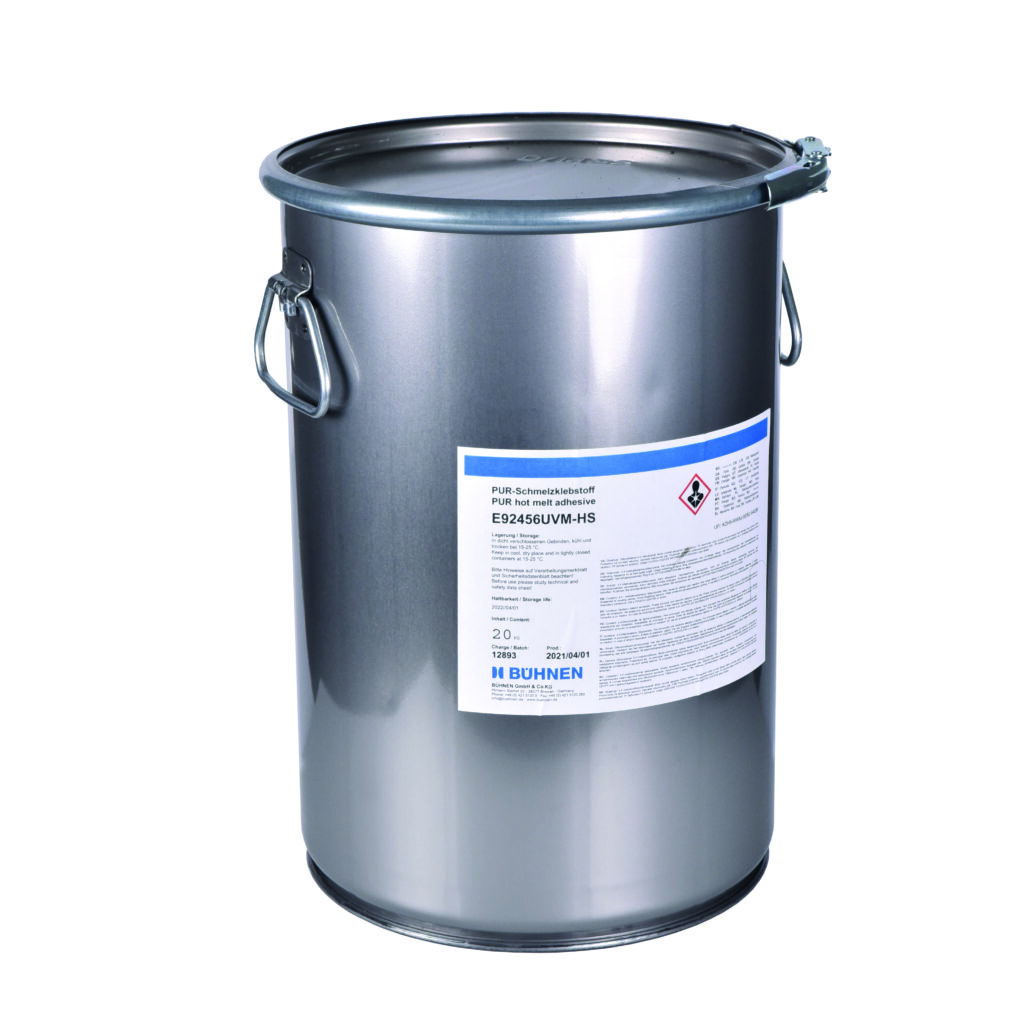
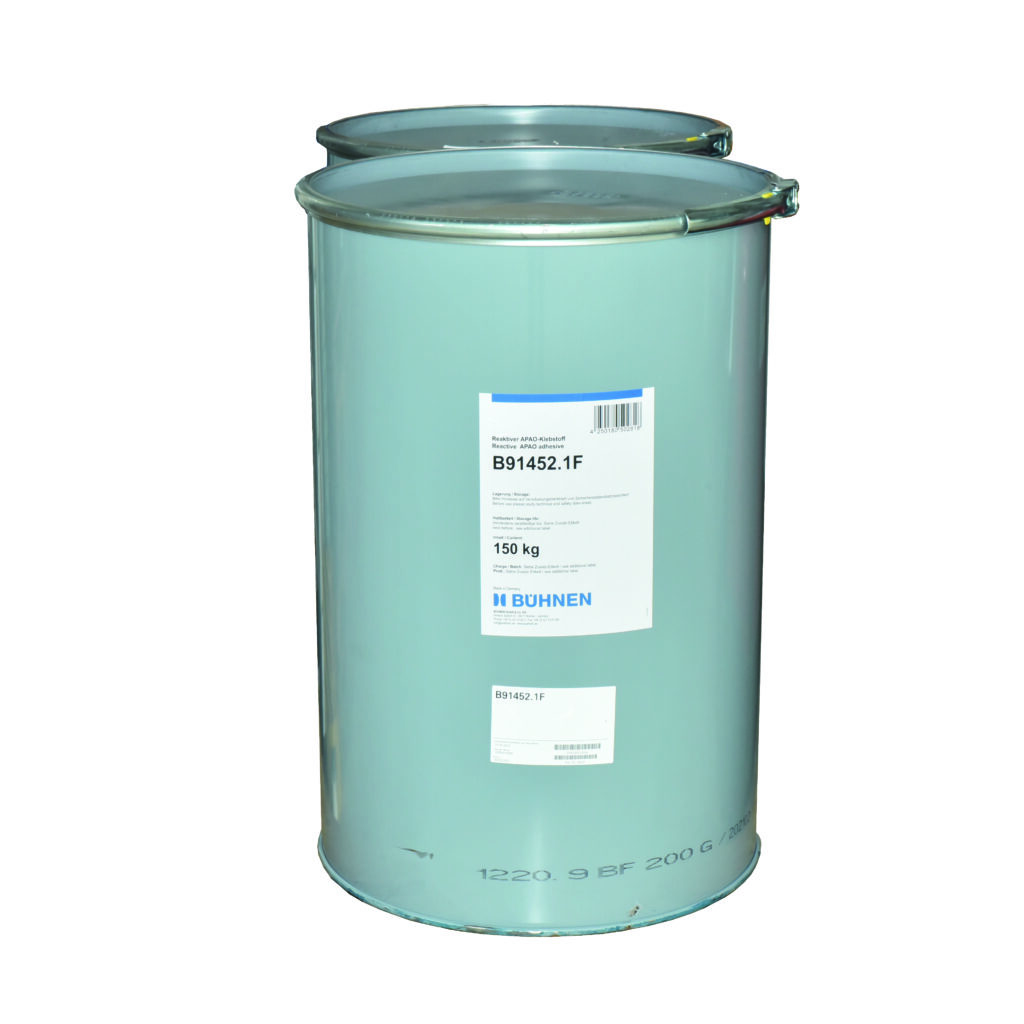
Application technology
The right tools play a decisive role when processing these adhesives. Reactive hot-melt adhesives are available from BÜHNEN on the basis of polyurethane (PUR) and polyolefin (POR). These hot-melt adhesives must be packaged in airtight containers.
Our HB 720 K pneumatic hand guns are ideal for the manual application of cartridges, while the HB 4000 connect series is suitable for larger containers, such as 2 kg units or 200 litre drums. Our melt tank equipment is equipped with a compressed air dryer to ensure that the adhesive does not prematurely cross-link.
The right application technology for all container forms
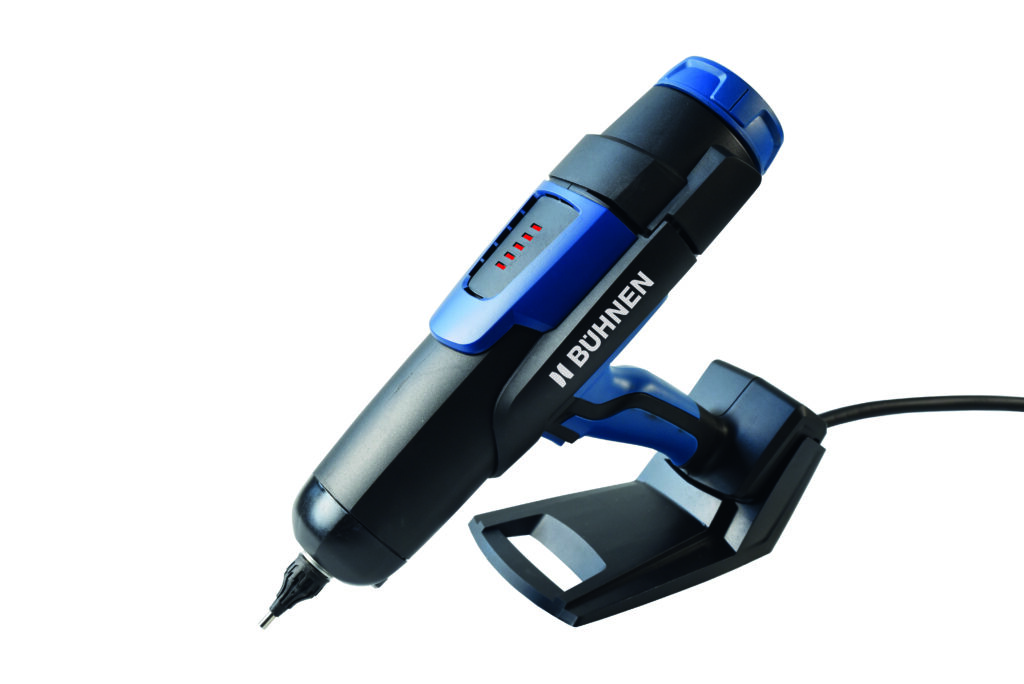
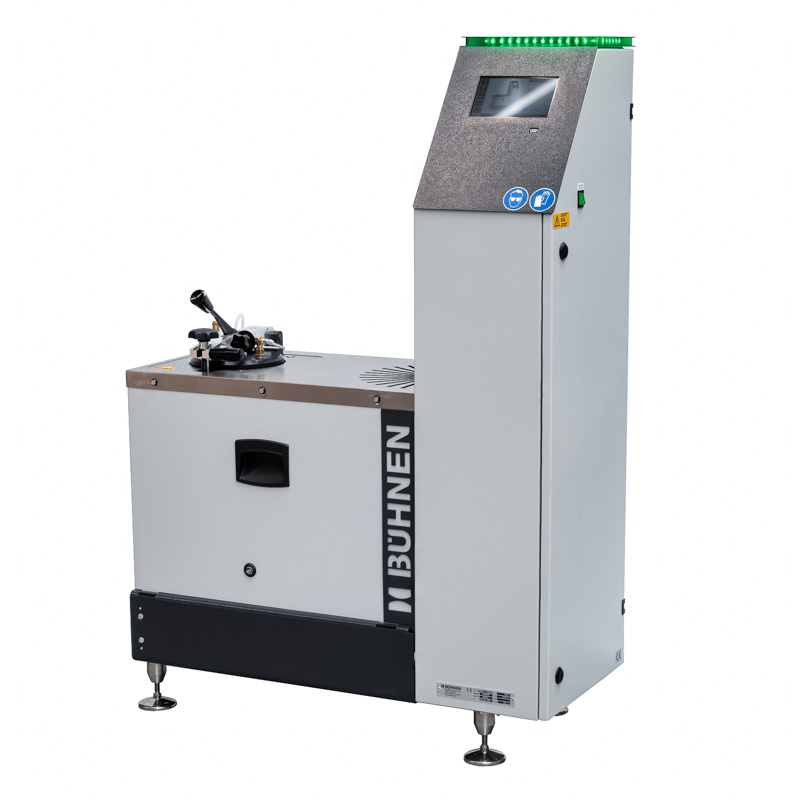
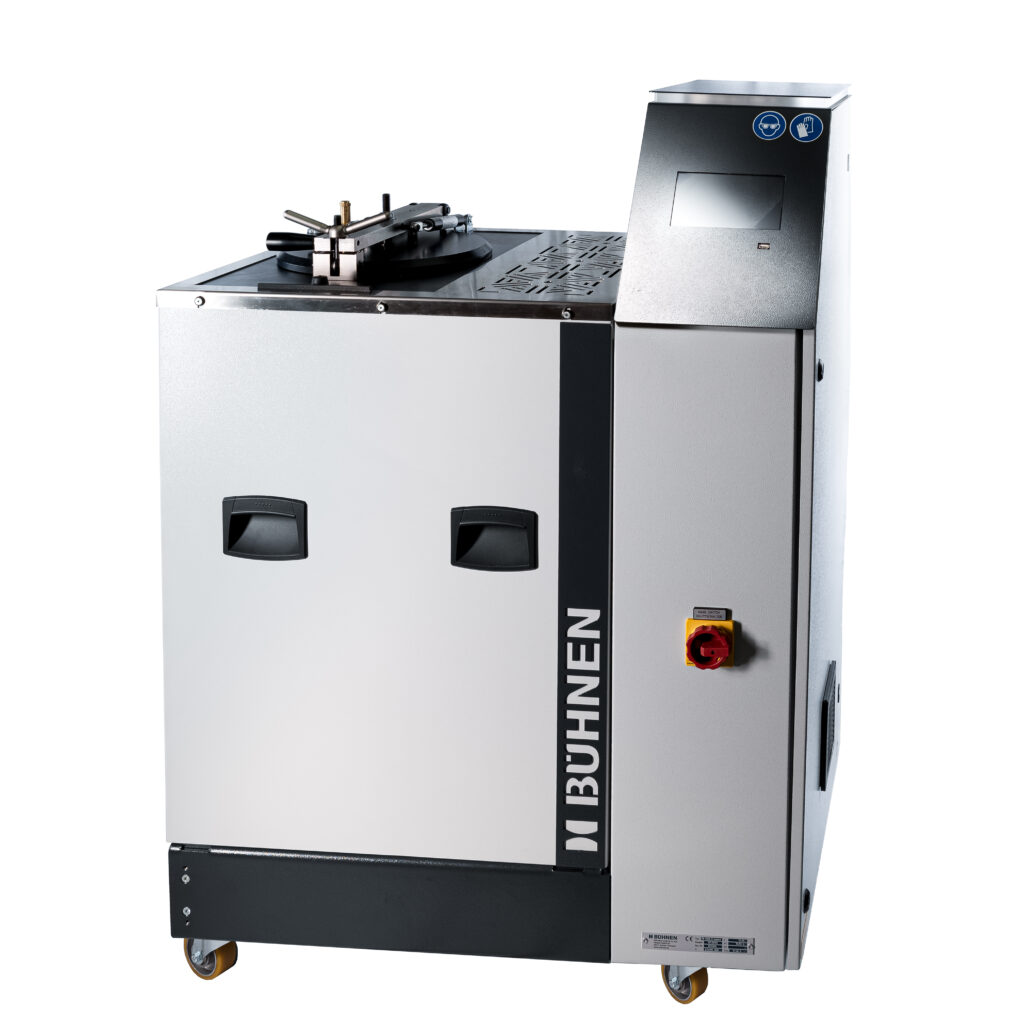
The areas of application for reactive hot-melt adhesives are diverse and range from the automotive, construction, textile and electronics industries to the furniture industry. Their versatility and performance make them an indispensable part of modern manufacturing processes.
- Our YouTube channel – knowledge to view - 6. Mai 2025
- Efficient adhesive supply with the granulate conveyor: How to optimise your production: - 15. April 2025
- Blocked hot-melt adhesive granules – causes, effects and solutions - 11. März 2025