PUR / reactive polyurethane
Combining the advantages of two adhesive worlds
High process speed plus high bond strength
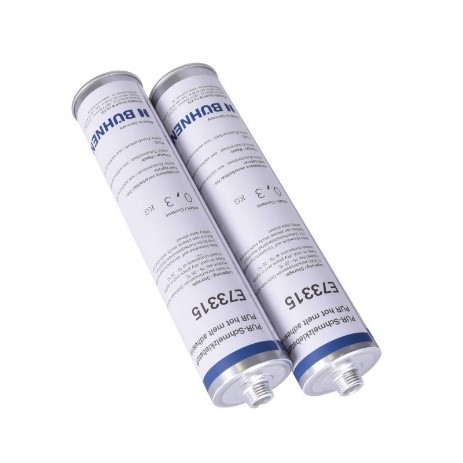
Polyurethane adhesive in cartridge
Polyurethane hot-melt adhesives are characterised by the fact that they combine the advantages of physically setting hot-melt adhesives with their high processing speeds, with those of reactive one/two-component adhesives and their high bond strengths.
This combination of properties has led to polyurethane hot-melt adhesives being used in a wide range of applications, such as in the automotive industry, filter industry, construction industry, wood and furniture construction, book-binding, packaging industry and textile industry, to name just a few important ones.
Polyurethane hot-melt adhesives are used by surface application for laminations in, e.g. the textile industry, as well as in bead application in, for example clip bonding in the automotive industry.
The reactive properties of polyurethane (PUR) hot-melt adhesives refer to the chemical process which occurs after the hot, liquid adhesive is applied and cooled. This process involves the curing or cross-linking of the adhesive and results in a permanent, strong and thermally stable connection.
Applying / bonding / joining with reactive hotmelts
As it is a reactive (moisture-curing) adhesive, the application technology must protect against moisture absorption; this, of course also applies to the packaging of the adhesive itself.
It has become standard practice for tank melters to be additionally equipped with air dryers or, as an alternative, bag, hobbock or drum melters without air dryers are also available.
At the same time, special heatable hoses and application heads are used for reactive adhesives.
Cross-linking and curing:
The cross-linking or curing of PUR hot-melt adhesives occurs under the absorption of moisture/water, in which the terminal isocyanate groups of the polyurethane resin react with the separation of CO2 and formation of urea groups to a macromolecule. The water can be absorbed from the ambient air or from the joined substrates through diffusion.
This leads to the formation of three-dimensionally macromolecules within the adhesive. The cross-linking and curing of the adhesive causes it to develop its final mechanical properties, such as tensile strength, hardness and thermal resistance (no longer meltable).
The reaction time / chemical post cross-linking is completed after 1 - 5 days (depending on the type), also depending on the ambient conditions (humidity and temperature).
The reactive PUR hot-melt adhesives are subject to the Hazardous Substances Ordinance for reason of the reactive isocyanate groups. Depending on the proportion of free isocyanate content, the classification ranges from labelling-free to labelling-required.
The range of gradation is as follows:
- ME – Micro Emission = <0.1 % free NCO– no labelling required, no training requirement
- LE - Low Emission = >0.1<1.0 % free NCO– labelling required, H351 omitted
- Classic PUR hot-melt adhesives = >1.0 < 5.0 % free NCO, labelling required
The trend is towards ME and LE PUR hot-melt adhesives.
Training requirements when working with LE and classic PUR hot-melt adhesives: Ensure that all employees working with reactive PUR hot-melt adhesive are appropriately trained and understand the necessary safety precautions.
Combination of reactive properties with the advantages of standard hot-melt adhesives
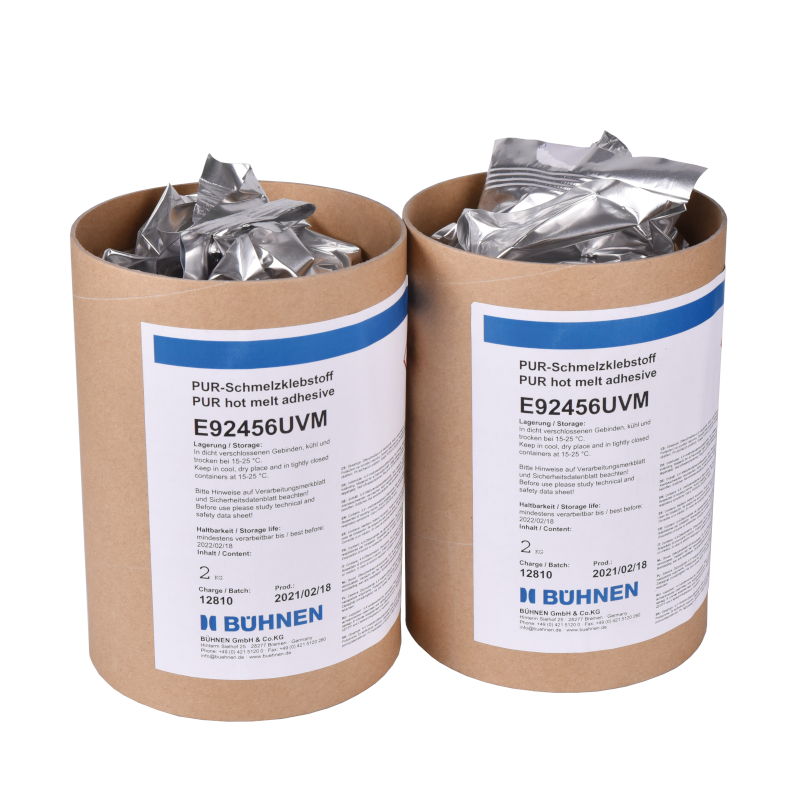
UV-marked PUR in 2 kg cardboard sleeve
PUR have a very broad adhesion spectrum. This is because these hot-melt adhesives have very low molecular weight when applied and joined, and therefore very good adhesion properties to many different plastics, e.g. ABS, PVC, polycarbonate, polystyrene. Reactive PUR hot-melt adhesives provide excellent adhesion to a variety of materials, including metal, plastic, wood and more. This results in long-lasting connection.
High cohesion enables constructive bonding. The reactive curing of PUR hot-melt adhesives leads to a strong and lasting connection between the bonded materials. This connection can provide resistance to tensile forces, shear forces and environmental influences.
High temperature resistance in both cold and heat enables e.g. use in the automotive industry.
Resistance to plasticisers, oils and solvents enables bonding of soft PVC and demanding filter applications.
High resistance to aging of the bond. Reactive PUR hot-melt adhesives are often resistant to UV radiation, moisture and other environmental influences, making them suitable for outdoor use.
Working with PUR hot-melt adhesive
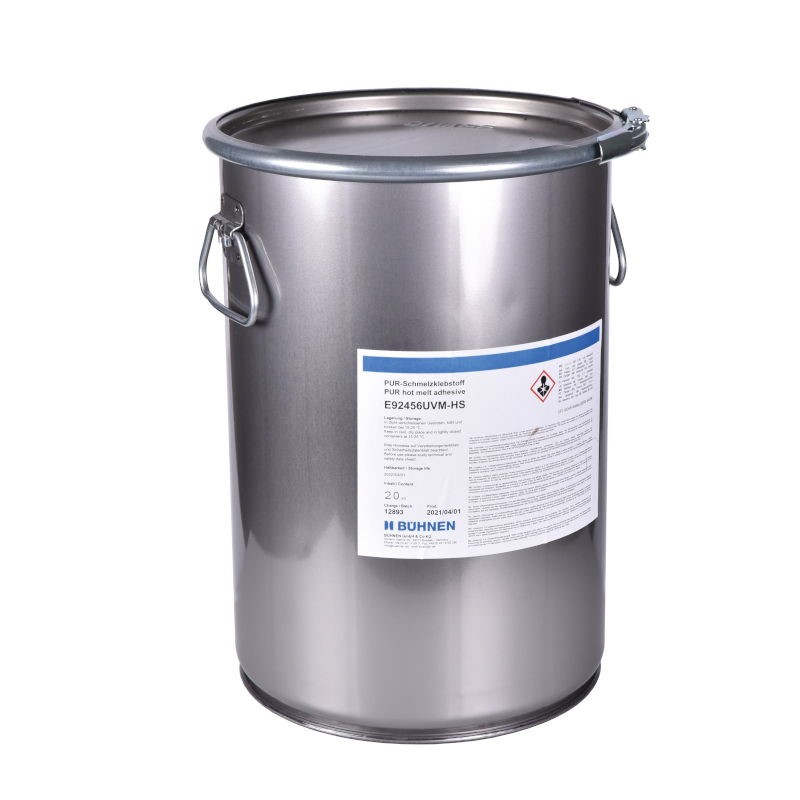
20 kg – Steel hobbock
Working with reactive polyurethane (PUR) hot-melt adhesives requires special precautions and knowledge to ensure that the adhesives are applied properly and that no health or safety risks arise. Here are some important points to bear in mind when working with reactive PUR hot-melt adhesives:
- Personal protective equipment: Wear suitable personal protective equipment, including safety glasses, gloves and, if necessary, respiratory protection, in order to avoid skin and eye contact and inhalation of fumes.
- Appropriate work area: Work in well-ventilated areas or under appropriate ventilation conditions to minimise the spread of vapours.
- Curing time: Take into account the curing time of the adhesive and ensure that the bonded parts are not disturbed during this time.
- Safety data sheets: Read the adhesive‘s safety data sheets carefully and follow the instructions contained in them for safe use, storage and disposal.
- Disposal: Dispose of used adhesive remnants and containers in accordance with local regulations and environmental requirements.
- Storage: Store according to the manufacturer’s recommendations, particularly regarding temperature and humidity, in order to ensure proper storage.